Abstract
IGBT modules as the preferred power semiconductor device are used widely for industrial
applications. The NX series with 6th generation IGBT using the latest CSTBTTM chip
technology realizes high performance-cost ratio. This paper will summarize how to use
CM450DX-24S for inverter applications with high reliability, which includes design details of
driver circuit and solutions to connecting IGBTs in parallel.
1 Introduction of 6th generation IGBT
1.1 The advantages of CSTBTTM chip
The latest developed 6th generation CSTBTTM uses high energy injection into the CS layer,
thin-wafer process, finer cells and structure optimization. Compared with 5th Generation
CSTBTTM, it provides the advantages of more than 10μs short circuit capacity and excellent
paralleling characteristics suitable for practical application.
1.2 Positive temperature coefficient of saturation voltage of 6th generation
IGBT
6th generation CSTBTTM chip employs the Light Punch Through (LPT) vertical structure,
which is based on NPT structure and adds PT structure element. Taking Mitsubishi
CM450DX-24S as an example, above approximate 120A, it has a positive temperature
coefficient which makes it simple to connect several CM450DX-24S in parallel.
2 Design details ofIGBT driver circuit
2.1 Galvanic isolation of DC/DC power supply according to different safety
standards
The basic requirement of developing
IGBT drivers is to ensure insulation voltage for product
safety and user safety. A typical implementation of
IGBT driver is shown in Fig. 1. The value
of insulation voltage for DC/DC power supply is determined by the safety standards of
IEC61800-5-1 or EN50178 for industrial applications. But there is also a simple method to
specify insulation voltage based on IGBT insulation voltage in the datasheets provided by
IGBT manufacturers. According to design requirements, basic insulation or reinforced
insulation needs to be selected firstly, and the main difference is that basic insulation only
provides protection against electrical shock, but reinforced insulation provides protection
against electrical shock and failsafe operation. Failsafe permits users to contact with product
under fault condition. When developing IGBT driver for 450A/1.2kV IGBT, basic insulation
can meet the insulation requirement what is defined by the section 4.2.3.2 of IEC61800-5-
1:2003. The section 5.2.3.2.2 of value and type of test voltage specifies test voltage, and
insulation voltage can be calculated according to the following equation:
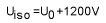
(In TN and TT systems, U0 is the r.m.s value of the rated voltage between a phase and earth;
in three-phase IT systems, U0 is the r.m.s value of the rated voltage between phases)
And we can also refer to the section 9.4.5.2.2 value and type of insulation test voltage of
EN50178:1997, which requires insulation voltage according to the following equation:
For example, for a two-level inverter with the allowed input line voltage range of 323VAC to
528VAC, 1200V IGBT modules are selected based on a maximum DC-bus voltage, resulting
from a three-phase rectified voltage plus a certain margin of the regenerated power of the
load possibly feeding back to into the DC-bus. Referring to IEC61800-5-1, as the input
voltage of DC/DC power supply is +15VDC, the input circuit of DC/DC power supply is defined
as Circuit A, and the output circuit of DC/DC power supply connected to IGBT can be defined
as Circuit C. If protection against direct contact is provided by supplementary insulation for
Circuit C, basic insulation should be designed to meet isolation requirement. According to
Eq.1, a Uiso of more than 1728VAC can meet isolation requirement. And according to Eq.2, a
Uiso is more than 1542VAC. While the insulation voltage of CM450DX-24S is 2500VAC, so it
could satisfy the requirement of basic insulation.
2.2 Selection of opto-coupler between IGBT and control signal according to
VIORM and VISO
To ensure the
inverter system safety, a galvanic isolation is required between IGBT and
control signal. When applying opto-coupler for circuit design, the parameters of VISO
(momentary withstand voltage) and VIORM (maximum working insulation voltage) are of
significant importance for circuits designers. The opto-coupler is basically certified through
the safety standards of IEC60747-5-2 and UL1577. UL1577 rating of VISO means that
devices can survive and isolate transient (1min) voltage spikes within its respective
requirements. This is only a momentary insulation withstand rating for one minute. The VIORM
is specified by IEC60747-5-2 rating, which means that the voltage can continuously apply
across the opto-coupler insulation barrier. When selecting the opto-coupler, major concerns
for designers are VIORM and VISO which are determined by the DC-bus voltage of inverter.
For example already described in chapter 2.1, a VIORM of 891Vpeak and a VISO of 3750Vrms or
5000Vrms of opto-coupler in the datasheets provided by Avago can meet isolation
requirement.
2.3 IGBT gate drives and protective measures
2.3.1. Comparison of different push-pull drivers (totem-pole drivers)
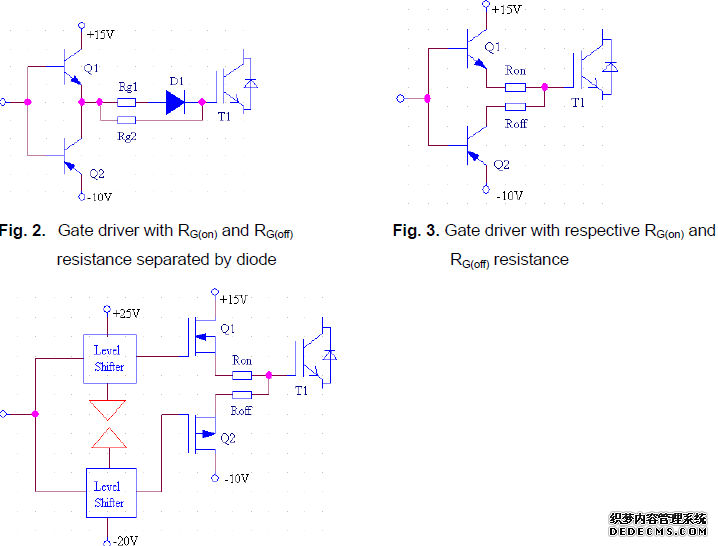
Fig. 4. Gate driver with the use of MOSFETs
Push-pull driver (totem-pole driver) with BJT or MOSFET is commonly used, which mainly
has three types shown in Fig. 2, Fig. 3 and Fig. 4.
The configuration of Fig. 2 is recommended for a push-pull driver, but Collector-Emitter
Voltage and Maximum Forward Bias Safe Operating Area need to be checked when
selecting NPN and PNP transistor.
The configuration of Fig. 3 is not recommended for a push-pull driver, as the base-emitter of
the transistor maybe has a breakdown under IGBT turned off or short circuit.
The configuration of Fig. 4 is sophisticated and we can apply MOSFET drivers and dual
channel MOSFET to design push-pull driver, or apply level shifter and buffer to design. When
selecting MOSFET, it’s more preferable to select n-channel MOSFET than p-channel
MOSFET, as the bulk resistance RDS(on) between the drain and source of the MOSFET per
chip size is lower compared to p-channel MOSFET resulting from the mobility of the hole and
electron.
The configuration of Fig. 4 has several advantages over the configuration of Fig. 2 as
follows:
Providing a rail-to-rail output, as the voltage drop between drain and source of
the MOSFET is nearly zero, we can set the output voltage of DC/DC power
supply to 15V, or else the output needs to be set to more than +15V;
Providing high gate currents for IGBT with high amplification gain and low control
current compared to gate drives using BJTs, and it can also replace what several
push-pull drivers with the use of BJTs are connected in parallel;
Reducing the turn-on losses of the IGBT due to higher switching speed of
MOSFET;
Using respective turn-on and turn-off resistors, the possible shoot-through current
can be limited from +15V to -10V, and switching characteristics of IGBT is easy to
adjust according to requirements.
2.3.2. IGBT protective circuits
As below is an overview of IGBT gate protective circuits, there are three typical protective
circuits as showed in Fig.5, Fig.6 and Fig.7.
Gate clamping circuit is to protect IGBT gate, as well as to limit short circuit current; active
clamping circuit is to limit VCE peak voltage at IGBT turned off; active miller clamping circuit is
to prevent the parasitic turn-on of IGBT.
Gate clamping circuit is shown in Fig. 5, the circuit consists of Zener diode and fast Schottky
diode. The function of Zener diode of DZ is to limit the maximum gate-emitter voltage less
than 20V, and fast Schottky diode of D1 is to clamp the gate-emitter voltage to the value of
the positive supply voltage plus the diode forward voltage, which has been proven extremely
useful under short circuit.
Fig. 6 shows one type of active clamping, which is commonly used to protect IGBT from high
voltage peak across collector-emitter of IGBT resulting from short circuit, overload current.
For practical design, the maximum active clamping voltage is set based on the RBSOA
diagram of CM450DX-24S, and the internal stray inductance of the module also need to be
taken into account; TVS diodes connected in series is recommended for active clamping
circuit.
Fig. 7 shows the type of active miller clamping which is used to prevent parasitic turn-on of
the IGBT due to the miller capacitance in single power supply gate drivers (0 to +15V).
Although this parasitic turn-on lasts a very short time, it can lead to larger losses in the IGBT
and cause the temperature of IGBT chip to rise. Finally, the IGBT may be broken down by
thermal runaway. This circuit has better use n-channel MOSFET to create a low-impedance
path, as BJT has a higher voltage drop across collector-emitter.
3 IGBT driver design for parallel connection of IGBTs
Parallel connection of IGBTs is commonly used for higher power applications. Three
CM450DX-24S connected in parallel could realize 250kW/380VAC inverter design. When
using IGBTs connected in parallel, the following design tips need to be concerned:
All the parallel connection of IGBTs are driven by the common driver;
The length of twisted pairs or PCB tracks are identical;
Resistor tolerance should be less than 1%;
Inserting a emitter resistor in series with each emitter to force current balance is
very important.
Fig. 8 shows two IGBTs in parallel connection. Due to parallel connection of IGBTs with
different tolerances, the IGBTs have different switching speeds. The fast IGBT1 causes a
higher di/dt, and a higher induced voltage across the emitter stray inductances of L1 will
occur. So a loop current flows through Re1, Re2 and L2 to L1.The gate voltage of IGBT1
VG1E1=VCC- VRe1 due to the voltage drop VRe1 across the Re1, and the gate voltage of IGBT2
increases up to VG1E1=VCC+ VRe2. As a consequence, the current of two parallel IGBTs
achieve symmetry. Based on application experience, the emitter resistor is recommended to
select pulse power resistor and approximate 0.5Ωor 50% of the gate resistance.
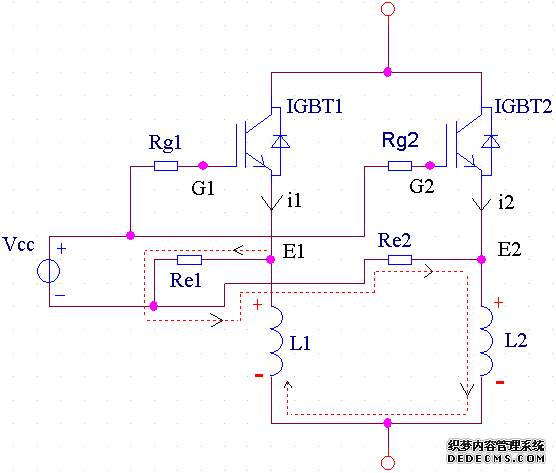
Fig. 8. IGBTs connected in parallel with the emitter resistors
4 Conclusion
The most important requirements that a reliable IGBT driver for CM450DX-24S has to
meet and perform simultaneously can be summarized briefly as follows:
a) An insulation voltage of 2500VAC is recommended for DC/DC power supply as
described in chapter 2.1;
b) A VIORM of 891Vpeak and a VISO of 3750Vrms or 5000Vrms is recommended for
opto-coupler as described in chapter 2.2;
c) Gate clamping circuit, active clamping circuit and active miller clamping circuit are
commonly used to protect IGBT under abnormal condition;
(文/上海合美电子科技有限公司)